Introduction to Safety Management System (SMS)
- What is a Safety Management System?
- Why a Safety Management System matters
- Safety Management System: The four key elements
- Why different industries need a tailored approach
- Common challenges in implementing a Safety Management System
- Digital platforms Help Streamline Safety Management System
- Best practices for adopting a digital Safety Management System
- Conclusion
Interested to learn more about Novade Safety Management System?
A safety management system is key to maintaining a safe, compliant, and efficient workplace. In this overview, we will explore what a safety management system is, why it matters, and how to implement its core elements across different industries. We will also look at common challenges, the role of digital platforms, and best practices for adopting a digital approach.
What is a Safety Management System (SMS)
A safety management system is a set of policies, procedures, and tools designed to protect workers, reduce risks, and comply with regulations. It provides a structured framework for preventing accidents and creating a safer working environment. By having clear processes and responsibilities, organisations can minimise hazards and respond effectively to any issues that arise.
Why a Safety Management System matters
Having a safety management system in place offers multiple benefits:
- Protects people
A well-implemented system helps employees, contractors, and visitors work without fear of accidents or injuries. - Reduces costs
Fewer incidents mean lower insurance premiums, reduced downtime, and fewer fines for non-compliance. Over time, a proactive safety approach can significantly cut costs. - Meets legal requirements
Most regions enforce strict workplace safety regulations. A clear system demonstrates your commitment to safety and helps you avoid legal issues. - Improves company reputation
Clients and partners value organisations that prioritise staff well-being. A strong safety record can lead to more business opportunities.
Safety Management System: The four key elements
A safety management system usually consists of four main elements: Safety Policy and Objectives, Safety Risk Management, Safety Assurance, and Safety Promotion. Together, these create a culture where everyone is committed to reducing hazards and preventing accidents.
1. Safety Policy and Objectives
A safety policy is a formal statement of an organisation’s commitment to safety. Objectives are specific goals and measurable targets to achieve that commitment.
Why It’s Important:
- Clarity: Everyone in the organization understands that safety is a priority.
- Direction: Guides decision-making, resource allocation, and everyday actions.
- Accountability: Management and staff have clear responsibilities for meeting safety goals.
2. Safety Risk Management
Safety risk management is the process of identifying hazards, analysing potential risks, and implementing measures to eliminate or reduce these risks.
Key Steps:
- Hazard Identification: Spotting hazards through site inspections, reporting tools, and regular feedback.
- Risk Assessment: Evaluating the chance and impact of potential incidents.
- Control Measures: Introducing protective equipment, safe work methods, or engineering solutions to mitigate risks.
3. Safety Assurance
Safety assurance involves checking if your safety management system is working properly and making improvements where needed.
Main Activities:
- Audits & Inspections: Formal reviews that confirm compliance and uncover gaps.
- Performance Monitoring: Tracking data on incidents, near-misses, and other safety metrics.
- Continuous Improvement: Updating procedures and training based on findings and best practices.
4. Safety Promotion
Safety promotion focuses on building awareness, knowledge, and a positive safety culture across the organization.
Core Components:
- Training & Education: Providing regular safety courses and job-specific drills.
- Open Communication: Encouraging employees to report issues and share ideas.
- Positive Reinforcement: Recognizing and rewarding safe behavior to keep people motivated.
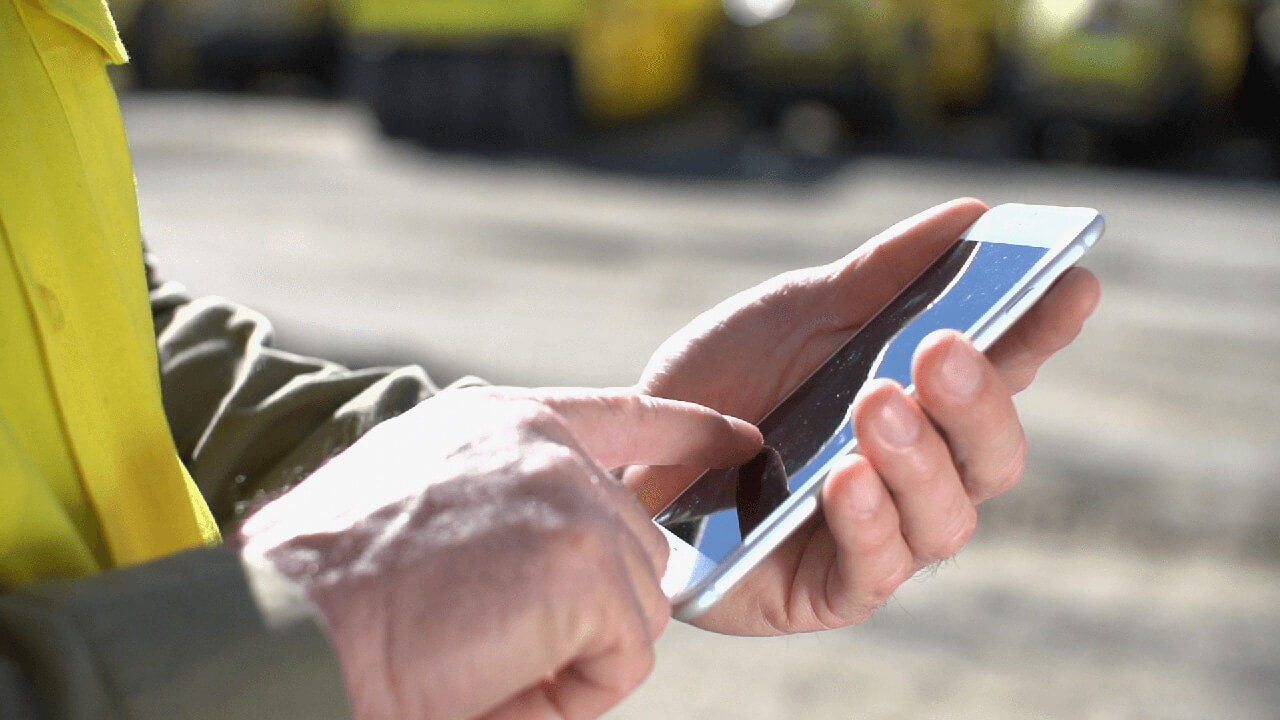
Why different industries need a tailored approach?
Even though these four elements are universal, each industry faces unique risks and regulatory requirements. Here’s a snapshot of why a safety management system needs to be adapted to different environments:
- Building Construction: Projects often involve shifting site conditions and multiple subcontractors, increasing the need for clear communication and daily risk assessments.
- Infrastructure: Work typically occurs in public areas like roads, railways, or bridges, so safety measures must protect both workers and the public.
- Energy: Handling high voltages, pressurized systems, or hazardous materials demands rigorous control measures and strict emergency response plans.
- Utilities: Supplying essential services (water, gas, electricity) requires reliable operations, thorough maintenance, and swift responses to any safety incident.
- Manufacturing: Assembly lines and heavy machinery need strict guarding systems, ergonomic considerations, and frequent inspections to prevent equipment failures.
- Industrial Sites: Large-scale operations with intensive workflows and complex equipment require regular audits to identify issues early and maintain a safe environment.
Common Challenges in implementing a Safety Management System
- Resistance to change: Employees may be hesitant to adopt new processes or report near-misses if a transparent safety culture is not already in place.
- Data overload & complexity: Large projects and sites generate substantial amounts of safety data, from inspections and audits to incident reports.
- Inefficient communication channels: If hazard reports and corrective actions are not shared promptly, critical safety information can be lost in the shuffle.
- Lack of continuous improvement: Safety is an ongoing process. Without proactive reviews, feedback loops, and updates, existing practices can quickly become outdated.
Digital platforms help streamline Safety Management System
Digital solutions offer a centralised, efficient way to manage safety processes. Key benefits include:
- Accessibility: Mobile apps enable frontline operators and site managers to report hazards, near-misses, or incidents in real time, ensuring immediate action can be taken.
- Time saving: automating tasks like inspections, alerts, and follow-ups saves time and reduces manual errors.
- Centralised records: Storing all safety documents in one place simplifies compliance checks and audits.
- Continuous improvement: Digital platforms can generate insights and recommendations, turning raw data into actionable steps to prevent incidents and refine safety protocols.
Best practices for adopting a digital Safety Management System
- Involve all stakeholders early: Engage teams at every level—executives, managers, supervisors, and frontline workers—when choosing and rolling out a new system.
- Prioritise training & onboarding: Provide comprehensive training to all users, ensuring they understand not just how to use the platform but why it’s beneficial.
- Set clear KPIs: Identify specific safety metrics to track (e.g., incident frequency, near-miss reporting rate, training completion rate) and use your digital platform to monitor progress.
- Regularly review & update: Technology and regulations evolve. Periodically evaluate whether your safety processes align with the latest industry standards and digital platform updates.
Conclusion
A safety management system is an invaluable framework for any organisation aiming to protect its people, maintain regulatory compliance, and reduce costs. By focusing on the four core elements—Safety Policy and Objectives, Safety Risk Management, Safety Assurance, and Safety Promotion—companies can build a robust safety culture that minimises accidents and boosts overall performance.
Digital safety solutions further strengthen these efforts by providing real-time data, streamlined reporting, and actionable insights. If you are keen to explore how a digital platform can enhance your safety management system, a solution like Novade offers tools to manage field compliance, inspections, audits and corrective actions tracking. It also allows to conduct analytical work to understand patterns and identify risks.
Interested to learn more about Novade Safety Management System?
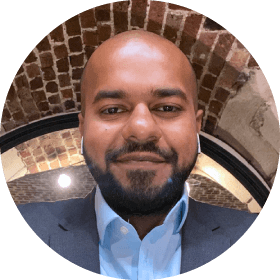
About Tejas Thomas
Tejas Thomas is the UK Country Manager at Novade. Based in London, Tejas specialises in helping clients in the construction industry harness the power of site data and analytics with cutting edge technology that improves quality, safety, and productivity. He also has experience in supply chain engineering and hi-tech manufacturing.
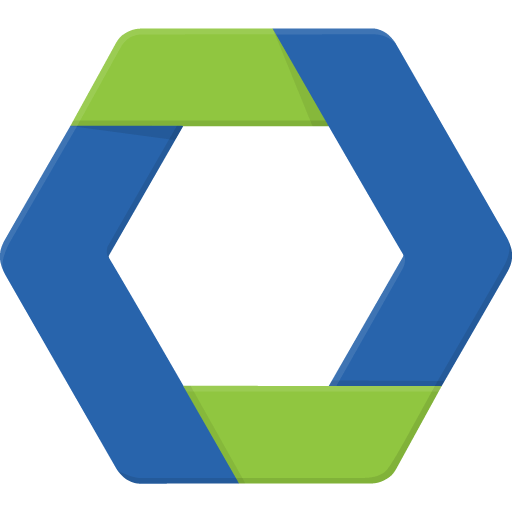
About Novade
Novade has a team of digital specialists dedicated to supporting clients in their digital transformation from the ground up. With global experience on a wide range of construction projects and processes, the team will be able to quickly adapt to your needs from specification through to delivery and on-site support.
Related content
- Learn more about Novade’s Safety module
- Learn more about Novade’s digital platform
See how Novade can help your safety process